石墨是一种重要的非金属矿物,经提纯后可在光学、能源、航天、环境、新材料等众多领域应用,因此,对其加工提纯具有重要的战略意义。石墨矿中常伴生有石英、伊利石、高岭石、红柱石、绢云母及少量黄铁矿、褐铁矿、电气石、和方解石等,需经提纯除杂才能应用,常见的石墨提纯方法有选择性絮凝法、浮选法、碱酸法、酸浸法、氯化焙烧法和高温焙烧法六种。
选择性絮凝法提纯石墨矿,需在含有两种及两种以上组分的悬浮液中,加入高分子絮凝剂,使絮凝剂选择性地吸附悬浮液中的某种组分,并通过桥链作用产生絮凝沉淀,从而达到组分分离的目的。
主要的絮凝剂有硅酸钠、六偏磷酸钠、木质素淀粉,羧甲基纤维素和水玻璃作为分散剂,木薯粉、橡子粉、海藻酸钠、聚丙烯酰胺作为絮凝剂对石墨矿进行提纯。
石墨矿选择性絮凝提纯法及设备都较简单,且成本低,但固定碳回收率较低,只有40%左右。
浮选是石墨矿提纯的常用方法,主要是通过添加一系列的浮选药剂来富集气液界面中所选的目标矿物,以实现与杂质矿物的分离从而达到提纯目的。
石墨本身具备良好的天然可浮性和疏水性,因此常规的石墨矿均可采用浮选工艺进行提纯。在提纯过程中,为保护石墨的大鳞片,工艺上一般采用多段磨矿、多次选别、粗精矿再磨再选的工艺流程。
石墨矿浮选法中常用的捕收剂多选用煤焦油,起泡剂多选用松醇油或丁醚油,抑制剂多选用水玻璃和氟硅酸钠。
石墨矿浮选法提纯可使石墨品位达到80%~90%,甚至是95%左右,且该方法药耗低、能耗低、成本低。但对于石墨矿中夹杂极细的硅酸盐矿物和钾、钙、钠、镁、铝等元素的化合物时,磨矿阶段不能实现单体解离,需在浮选法后使用其他工艺再次提纯。
酸碱法提纯石墨矿是目前较为成熟的工艺方法,可分为碱熔和酸浸两个过程。
碱熔过程:在高温条件下,利用熔融状态下的碱和石墨中的酸性杂质(硅酸盐、硅铝酸盐、石英)发生化学反应,生成可溶性盐,再用洗涤法去除杂质。
酸浸过程:利用酸与金属氧化物杂质发生反应,将碱熔过程中部分没有发生反应的杂质转化为可溶性盐,再经洗涤法去除杂质使其与石墨分离,以提高石墨纯度。
石墨矿碱酸法提纯可使石墨品味达到99.5%,且设备简单、能耗低、一次性投资小。但该种方法的酸碱会对设备有较强的腐蚀性,提纯后的废水污染严重。另外,还存在石墨流失的弊端。
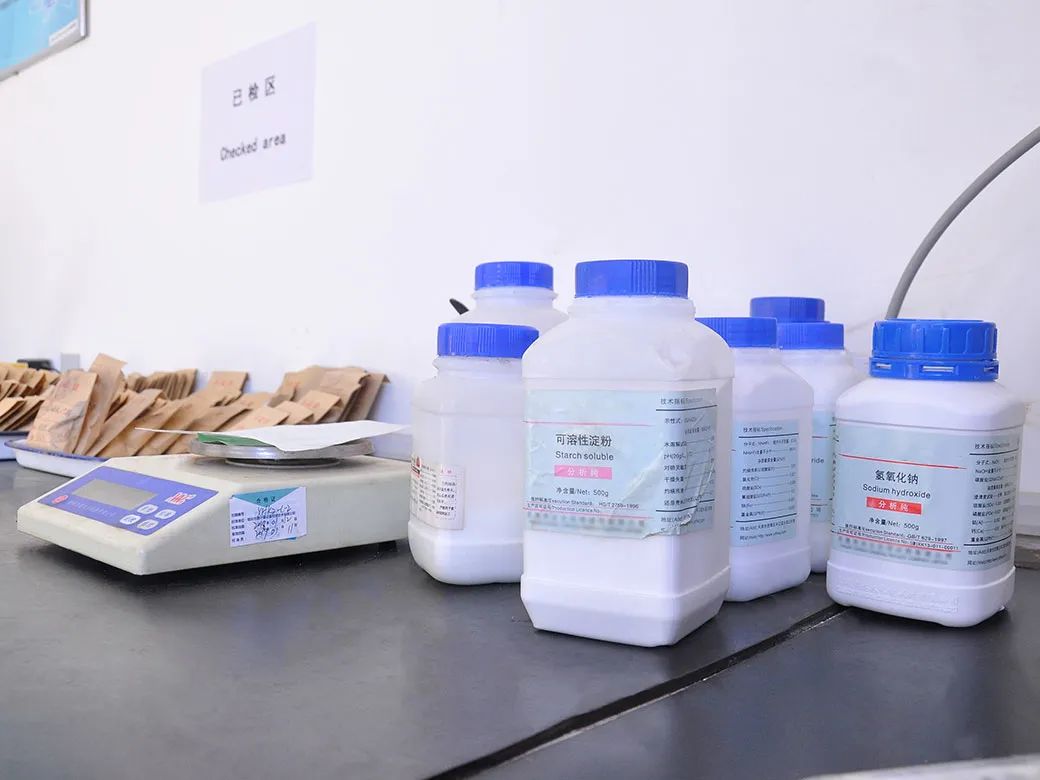
酸浸法提纯石墨矿使用的酸有硫酸、盐酸、硝酸、氢氟酸等。其中,硫酸和盐酸较适宜做浸出酸,浸出能力强,但有些硫酸盐溶解度较小,而盐酸价格较高;硝酸氧化和挥发性较强,见光易分解且易产生剧毒性光气,在高温下易爆炸;氢氟酸不能发生氧化反应,也不能进行还原反应,重点是能有效溶解SiO2和硅酸盐,将石墨与氢氟酸充分混合后,氢氟酸会与石墨中的杂质反应,生成溶于水的化合物和挥发物,再经过水洗法去除其中的可溶性杂质,即可得到高纯度石墨。
石墨矿氢氟酸法提纯能有效去除矿物中的杂质,且能耗低。但该方法有剧毒,环境污染较大。
氯化焙烧法提纯石墨矿,主要是在石墨矿中加入适量的还原剂,然后在特定的气氛和设备下高温焙烧,使矿物中有价金属与氯结合后,转变成低熔点沸点的气相或凝聚相金属氯化物,从而析出并实现与其他组分的有效分离,获得高纯度石墨。
氯化焙烧法提纯石墨矿效率高、且能耗低、成本低等。但该方法中氯气有较强的腐蚀性和毒性,对环境污染较大。
石墨矿的熔点非常高(熔点为3652℃,沸点为4250℃),其远高于其他杂质矿物。高温焙烧法提纯石墨是利用石墨的熔点差异进行选别的,将石墨矿加热到2700~3000℃,其中大部分的杂质已经气化,因此能有效将石墨与杂质分离。
高温焙烧法提纯石墨矿可将品味达到99.99%甚至更高,但能耗大、对设备的要求非常高,另外对石墨原矿的纯度有一定要求。
以上便是常见的6种石墨矿提纯方法,至于选择哪一种,需根据石墨矿的矿石性质、选厂条件、投资预算等多种因素来决定。建议选择工艺时,先对石墨矿进行选矿试验,通过试验报告具有针对性地选择提纯工艺,以争取理想的技术和经济效益。